|
|
January 12, 1999
Letter 8: Power, Water, and Food
Dear Everyone,
Power failure at the Amundsen-Scott South Pole Station is considered an
emergency situation because without it there is no heat, water resupply
nor the ability to cook. When there is a power failure, everyone is
expected to remain where they are and if an outside door is opened
letting in frigid air further dropping inside temperatures, they are
"cased". Casing is an informal fine requiring the provision of a case
of beverages purchased from our tiny window service store (called the
"Pole Mart") which is open only a couple hours a few times a week. This
case then is taken to the weekly Saturday afternoon department meeting
or the station meeting to be shared. Power conservation and power failure
is taken very seriously at our station.
Several nights ago I came to the dome early and was thrilled to be given
a tour of the power plant by Mike who will be the winter-over station
manager. The power plant is an "authorized personnel only" facility in
an enormous archway connected to the dome. Once entering the front office
area, Mike gave me a brief overview of what we would be seeing inside the
plant and explained the various functions of the main control panel. After
donning hearing protection devices, we entered.
Inside the power plant are 3 Caterpillar diesel generators Model #3412 at
563 horse power with 2 smaller emergency backup generators outside the dome
area located at the Jamesway (canvas Quonset tent) summer camp. Generally
the 3 primary generators run one at a time in rotation with the generators
at summer camp being used only as a last backup system. The generator's
turbo chargers are not able to produce their rated capacity due to the lack
of oxygen at our altitude. Each of the 3 main generators runs at about
1,800 RPM with an output of 400 KW of power. If there is a power loss,
an emergency start-up of another generator occurs. Typically a generator
requires 30 gallons of JP8 diesel fuel per hour at the cost of
approximately $7.00 per gallon. Although 2 generators can be in operation
at the same time, with both running there would not be enough JP8 to
survive the long and extremely cold winter months before it is safe for
the Hercs to fly in a station resupply. Around 300,000 gallons of fuel is
needed for the winter season. Because the emergency generators at summer
camp are smaller, the 2 could be run in parallel to provide the dome with
power for a short period of time until the main generators are functional.
Fuel is transferred to the primary operating generator every 2 hours from
the fuel bladders in the fuel arch that is connected to the dome opposite
the power plant archway. This season a series of 45 steel tanks for fuel
storage are being installed to replace the rubber bladders used in the
past. Nearly half a million gallons can be stored in this nearly completed
new facility. All year every 2 hours trained volunteers check the power
plant for functioning fuel transfer, generator mechanical function,
generator oil levels, and the even distribution of power over the station's
3 phases.
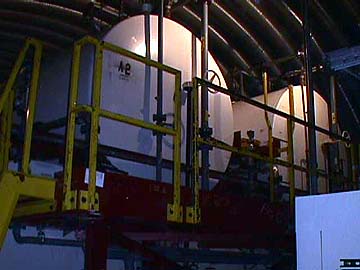
New steel fuel tanks in the fuel arch.
Photo by Les Kolb.
Station water supply is closely linked to the power plant. Prior to 1992
water was created by using snow melters. With increasing station population
and interest in the conservation of power, the station began implementing
the Rod well method for water supply. The Rod well was pioneered in
Greenland by Rodriquez for whom this method is named.
The generator exhaust stack in the power plant heats a glycol heat
exchanger and is pumped through a loop in the power plant itself. It then
heats water in a loop within the power plant through another heat exchanger
and circulates it to the Rod well where it melts ice for water. Cold water
of 36 F is drawn from the Rod well and heated to around 75 F at the rate of
17 gallons per minute and is pumped back down into the well in this loop
phase system to melt the ice and create a bulb of water. A submersible
pump then pumps it back up to the power plant where it is heated with
generator exhaust and returned to the well to melt more ice for water
in a continuous loop cycle.
The tremendous advantage of the Rod well is that it saves a great deal of
energy translated to money over the snow melt system. The heat value of
fuel is roughly 1/3 energy which is used for station electricity, 1/3 heat
(engine jacket temperature like radiator heat used to warm a car) which is
used to heat our buildings, and 1/3 exhaust heat which is used for the Rod
well to melt the ice for our station water supply. This method is 86%
efficient. The significant cost advantage of the Rod well water supply
system is that it requires no fuel, no major equipment and no operators.
Because the snow melt method of water production using fuel fired boilers
relies on fuel consumption, personnel and heavy equipment, it is very
expensive. The Rod well method has been used exclusively beginning in 1998.
The Rod well is around 60 feet wide and 415 feet deep and contains
approximately ² million gallons of water. The bulb descends as the ice
well melts down but the diameter remains quite uniform. The limit on the
well is how deep it is possible to pump up the water. The well's
submersible pump is approximately 300 feet below the surface. Once the well
becomes too deep to pump, a new well needs to be started. The life of a Rod
well is about 6-10 years. Depending upon need, the service of a Rod well is
approximately twice a year. This roughly entails pulling up the pump and
using a water jet to keep the ice from closing the hole that was bored
into the snow pack for the well. This process is called "reaming the well".
Station water use is approximately 2,000 gallons per day at 13-17 gallons
per person per day in the austral summer season and 25-30 gallons per
person per day in the winter season. This summer-winter use factor is
primarily due to the ratio of personnel to the galley for water use and
includes all water use (drinking, bathroom, and galley) for the station.
Station water is tested periodically and is chlorinated for the control
of bacteria in the insulated and heat trace warmed piping system.
Power and water are expensive at the Amundsen-Scott South Pole Station and
conservation is continually stressed. Lights are off when not in use and
the hallways are rarely lighted in the berthing areas. Bathroom lights are
habitually turned off when leaving. Laundry is limited to one load per
person per week. Full loads only are highly encouraged. This works out well
for Les and I because we can make one load of lights and the other of darks
rather than launder everything together. Although we use the washer we do
not use the dryer. This has a two-fold benefit. It not only saves energy
but also adds greatly needed humidity into the air of our room while we
sleep at night. Because of this need for the comfort of humidity, we
usually do our laundry before we go to bed and drape it over any available
space in our room. It's not very attractive but it saves energy, we sleep
comfortably, and it is dry and ready to put away when we wake up. Showers
are limited to two 2-minute "navy" showers (wet down, water off, soap up,
rinse) per week. Shower days are special even if the navy method is cold
when the water is turned off! Sink water is conserved by not letting water
run while brushing teeth or washing up. It is recommended that toilets not
be flushed after every use. In the Elevated Dorm gray water (recycled and
chlorinated water from the washing machine, sinks and showers) is used for
flushing.
Due to extremely low humidity and high altitude, personal dehydration is a
constant concern. Our station meteorologists tell me that our humidity is
usually between 5 and 10% and can be less than 5%. Water conservation is
practiced except in the case of personal water consumption. Here at the
South Pole Station it is recommended that we drink 4 quarts of water each
day whereas at McMurdo (sea level) 2 quarts daily are suggested. One of
the first symptoms I experience when not drinking enough water is a
headache. Especially during the first several weeks after our arrival, I
frequently woke up during the night with a dry nose and mouth in spite of
more than a gallon of water the 2 humidifiers we brought with us put into
the air of our small room. I still keep my water bottle propped in the
corner of my bed when I sleep so I can easily take sips of water during
the night. Due to the extremely dry air, bloody noses are not uncommon.
Before deploying to the ice, everyone was issued a plastic quart-sized
water bottle. Since these water bottles are all alike we have become
creative with permanent markers, colored tape and labels to aid in their
identification.
Like our fuel supply, our food is also aircraft cargo to the ice. Obviously
we do not need freezers for food storage, but we do need refrigerators to
prevent fresh or defrosted food from either freezing or spoiling. When we
say we're going to the freezer to pull a case of coffee or tea, that means
we're going outside a building in the dome to the area inside the dome.
Cases and bags of food are stored in all available spaces around the inside
wall of the dome and behind and around the sides of some of the buildings.
Foods are grouped according to type and in some instances are alphabetized.
For example, the cases of canned and bagged fruits and vegetables are
grouped in one area and the meats and seafood in another area of the
dome.
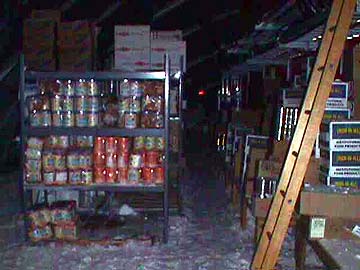
Frozen food stored around the buildings inside the dome ("the deep freeze").
Photo by Les Kolb.
There is a room in the dome near the galley called the "Freshie Shack" that
is heated to 40 F for the storage of fresh fruits, vegetables, and dairy
products should we be so fortunate to be designated freshie cargo. Our last
supply of significant size was just prior to our Thanksgiving dinner. Since
then we had a small order of several cases that exhausted itself within a
few days. We had no freshie cargo for Christmas and none since that I can
determine. Yesterday one of the cooks told me that there would be no more
freshie delivery this season. Our fruit supply is down to canned apricots,
applesauce, plums, fruit cocktail, and some grapefruit. The canned
grapefruit will not last much longer. There are frozen blueberries and
other assorted berries that the cooks use in baking or add to the yogurt
they make and serve at breakfast. The frozen melon balls have not been
too popular so I believe the cooks are reluctant to serve them.
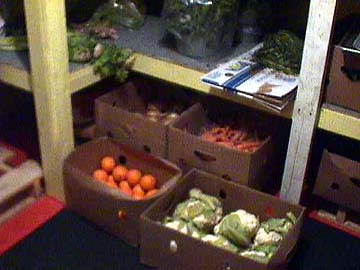
Freshies inside the Freshie Shack.
Photo by Les Kolb.
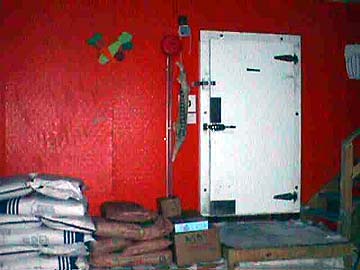
The entrance to the Freshie Shack (inside the dome).
Photo by Les Kolb.
Meals are generally planned a week ahead of time and the cooks keep
shopping lists with the help of the cook's assistant of the cases of foods
that need to be pulled from the "freezer". These frozen foods must be
pulled well ahead of time to allow for defrosting. They are frozen
extremely hard. It takes ages for ice cream to thaw enough to scoop with
ease! When the cook's assistant goes to the freezer to pull cases of food,
we call it "going shopping". Along with the shopping notebook and generally
pulling a banana sled, the cook's assistant goes from area to area inside
the dome selecting the cases of food to be carried into the galley pantry
to thaw for use in the following day or days.
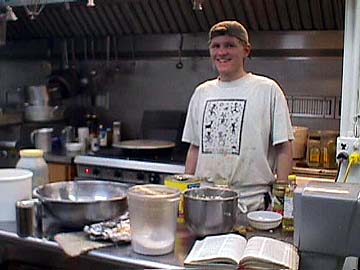
Mark, our breakfast and lunch first cook, in the galley.
Photo by Les Kolb.
Our excellent night cook, Laura, and the baker, Marcie, tell me that the
galley uses 100 lbs. of flour per day. Marcie bakes all of our bread
including hamburger buns. Both Marcie and Laura bake fresh bagels,
croissants, donuts, scones, English muffins, cinnamon rolls and quick
breads on various days for our breakfast. Along with the 100 lbs. of
flour per day, the galley uses 30 lbs. of butter and 20 lbs. of margarine
in food preparation not to mention the quarts of vegetable and olive oil.
Every two days the galley goes through 30 lbs. of sugar. Sally, the galley
supervisor, tells me that approximately 80 lbs. of meat is served at
dinner, 40 lbs. at lunch, and 20 lbs. at midrats daily. If we were so
fortunate to have fresh potatoes, about 60 lbs. would be served at dinner.
About 30 lbs. of rice is used when served at dinner.
Future letter topics will be on science research projects at the Amundsen-
Scott South Pole Station, distinguished visitors, and the people working
here for the austral summer season.
If you are a science or math teacher and could use semi-rare data of ozone
profiles in table format for mini-projects to compare old data and
techniques and to identify/compare differing methods of collection or to
compare seasonal and annual data for your classes, then send an e-mail to
Elke Bergholz at: berghoel@spole.gov. Elke is a teacher who is working with
projects in ozone and climate monitoring here at the South Pole. She will
send you data collected over 3-4 times, some seasonal data and 1-2 annual
data reports. Elke said if you are interested in such data for classroom
use, she will add your name to a group mailing list.
For the latest on the adventures of the CBS TV crew still in Antarctica and
their visit to our South Pole Station, check out their web site at:
http://www.cbs.com/navbar/news.html. Click on the Antarctica icon and enjoy
the photos and vignettes.
Following is the December 1998 Climate Summary report prepared by Dar and
John, two of our station meteorologists.
Best regards,
Sandi
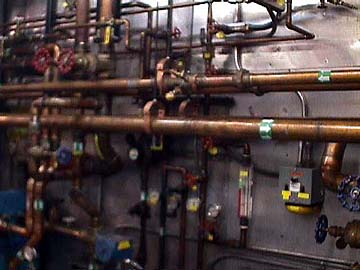
Rod well loop phase system in the power plant.
Photo by Les Kolb.
Rod well system in the power plant.
Photo by Les Kolb.
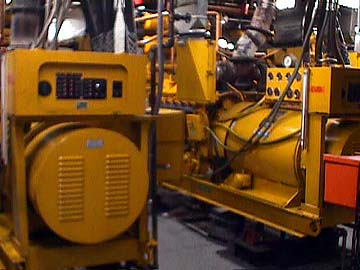
Caterpillar diesel generators in the power plant.
Photo by Les Kolb.
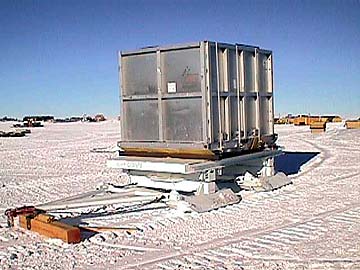
The water sled of Rod well water for the resupply of the Elevated Dorm and Summer Camp.
Photo by Les Kolb.
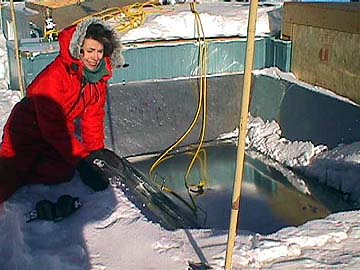
Sandi by an old snow melter for water supply at a summer camp head module.
Photo by Les Kolb.
SOUTH POLE STATION ANTARCTICA. DECEMBER 1998 CLIMATE SUMMARY.
Temperature:
Avg temp................ -29.0(C)/-20.2(F)
Departure from normal... -1.2(C)/-2.2(F)
Max temp................ -22.2(C)/-8.0(F) on day
4
Min temp................ -34.8(C)/-30.6(F) on day 25
Sky cover:
Avg cloud cover (8ths).... 05
Days clear................ 11
Days partly cloudy........ 10
Days cloudy............... 10
Wind:
Avg wind speed............ 7.1 mph or 6.2 kts.
Prevailing wind direction..Grid Northeast or 030 degrees.
Max wind.................. 25 mph or 22 kts on day 02
Max wind direction........ Grid Northeast.
Avg vectored wind......... 030 degrees at 4.9 knots.
Station pressure:
Avg pressure........... 684.4 mbs or 20.210 In. Hg.
Departure from normal.. - 4.1 mbs or -0.121 In. Hg.
Highest pressure....... 693.7 mbs or 20.485 In. Hg. on day 01
Lowest pressure........ 671.0 mbs or 19.815 In. Hg. on day 09
Sunshine:
Sunset on 21 March, Sunrise on 23 September
Average hours/day........ 20.2
Percent of possible...... 84%
Snowfall..... trace; avg net change at snow stakes +0.070 inches.
Visibility... 0 days with a visibility of 1/4 mile or less.
Balloon flight data:
Number of Soundings for the month... 61
Avg height of Soundings.... 34.4 mbs or 26863 meters above msl.
Highest Sounding........... 5.3 mbs or 36369 meters above msl.
on the day 12/00z Sounding.
Remarks:
1 Sounding was missed.
47 Soundings were terminated above 50 mbs.
8 Soundings were terminated between 50 and 100 mbs.
6 Soundings were terminated below 100 mbs.
Records:
Day 1 - The maximum temperature of --23.8(C)/-10.8(F) broke the
previous record of -23.9(C)/-11.0(F) set in 1965.
Day 25 - The minimum temperature of -34.8(C)/-30.6(F) broke the
previous record of -33.1(C)/-27.6(F) set in 1993.
Day 29 - The minimum temperature of -31.7(C)/-25.1(F) broke the
previous record of -31.1(C)/-24.0(F) set in 1962.
Day 30 - The minimum temperature of -31.9(C)/-25.4(F) broke the
previous record of -31.7(C)/-25.1(F) set in 1972.
Day 31 - The minimum temperature of -32.0(C)/-25.6(F) broke the
previous record of -31.1(C)/-24.0(F) set in 1972.
Prepared by: Dar Gibson/John Gallagher
e-mail: KOLBSA@spole.gov
amateur radio: NE7V
Sandra Kolb,ASA
South Pole Station
PSC 468 Box 400
APO AP 96598-5400
Back to Letters.
|